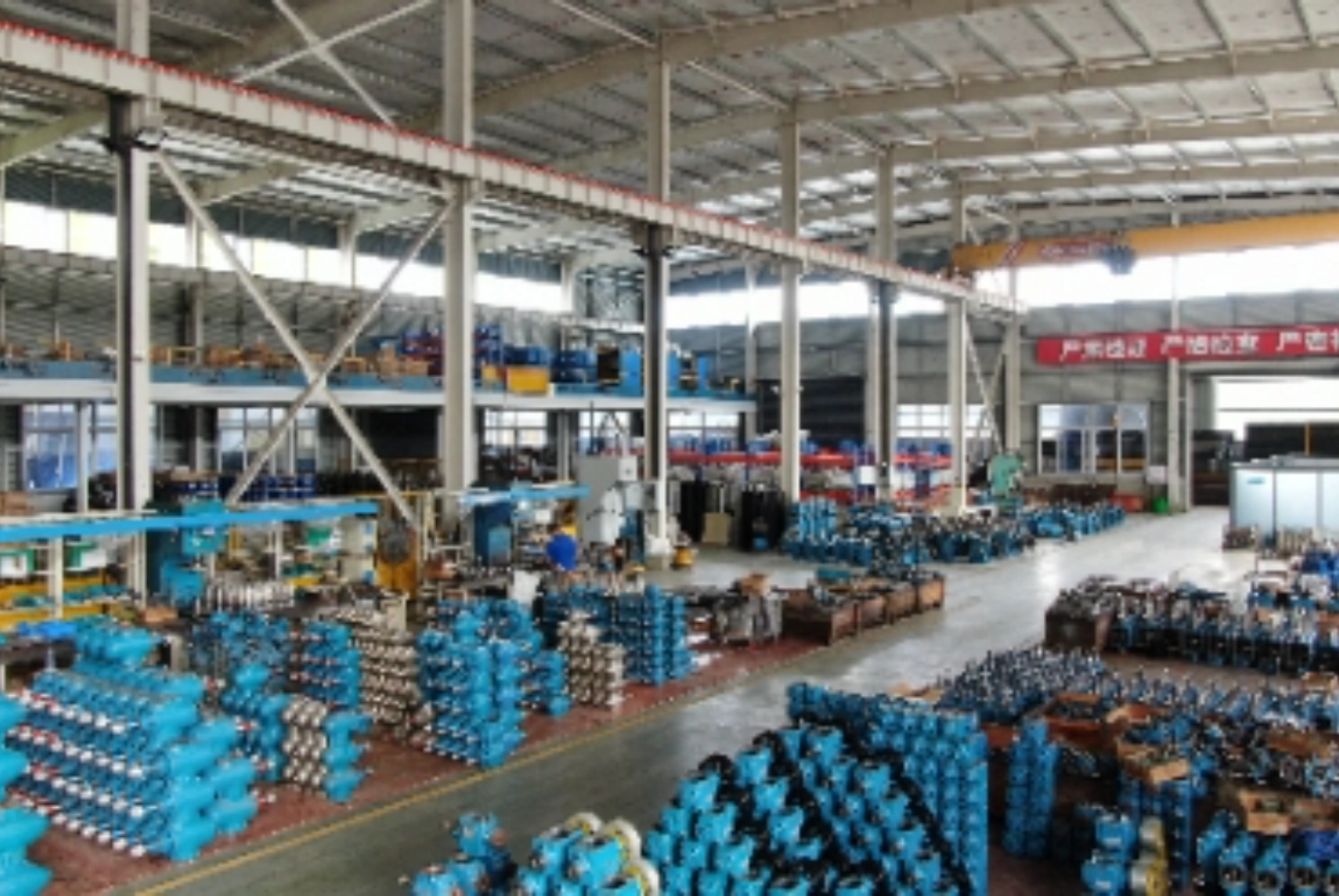
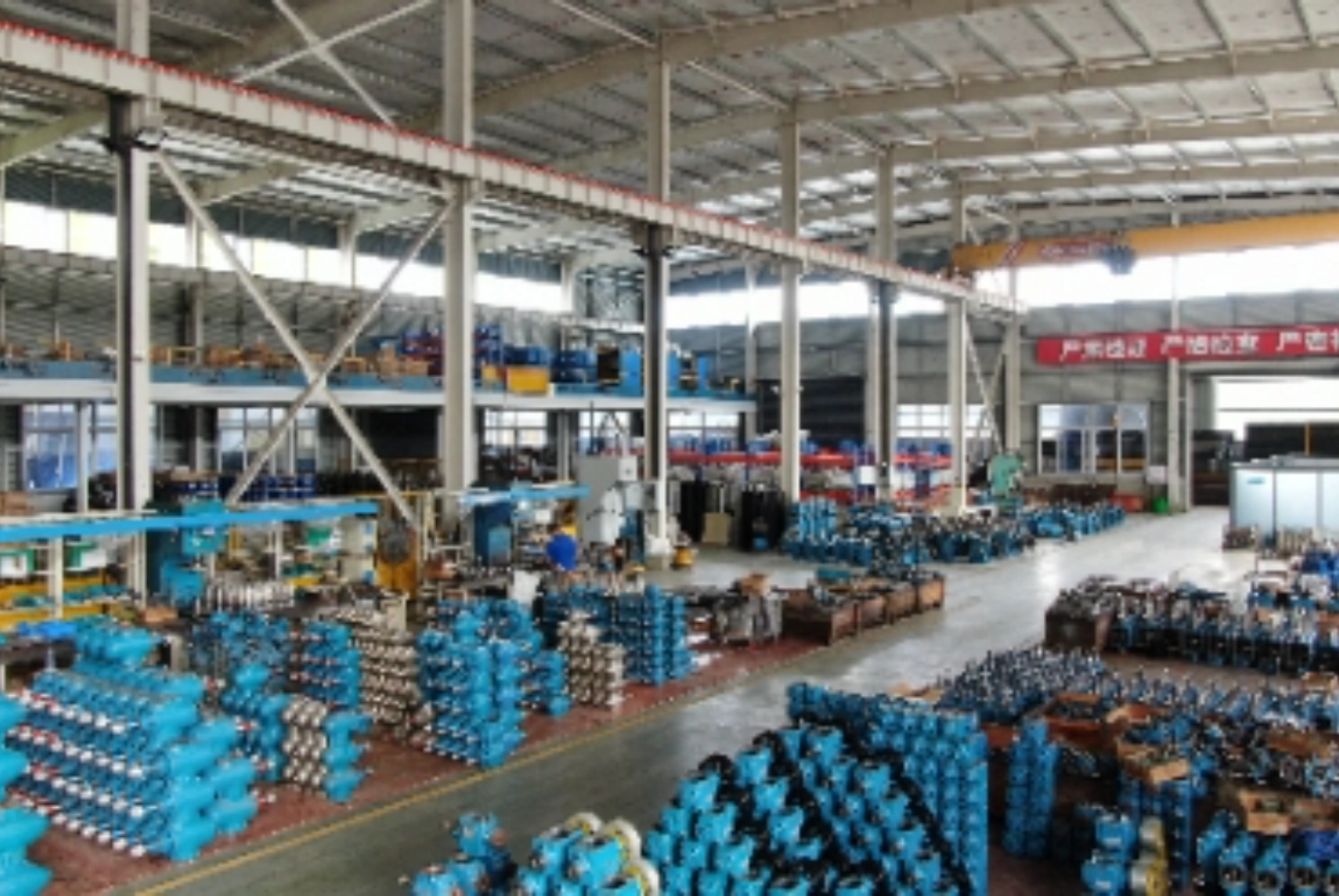
Glass shape edging machine play a key role in modern glass processing. They are designed to polish and finish the edges of glass pieces in various shapes. These machines improve the appearance, safety, and quality of glass, making them ideal for industries such as construction, automotive, furniture, and electronics.
Challenges in Glass Shape Edging Machine
Variety of Shapes
Today’s market demands glass in many shapes, including curves and complex designs. Traditional straight-line edging machines cannot meet these needs.
Precision and Consistency
Smooth and even edges are important for both safety and appearance. Manual methods often lack the accuracy needed for consistent results.
Efficiency
Large-scale production requires machines that can work quickly and handle big volumes. Older systems are often too slow and labor-intensive.
Safety Risks
Unpolished edges are sharp and dangerous. Poor edging can lead to injuries during handling and installation.
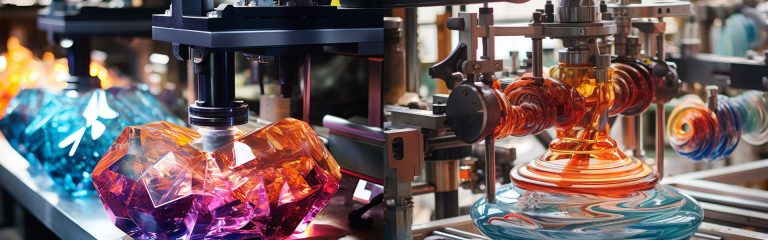
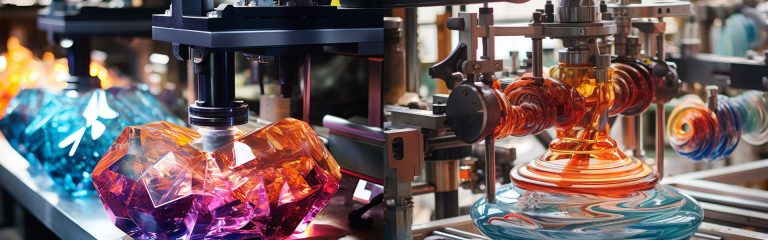
How Glass Shape Edging Machines Solve These Problems
- Multi-Shape Capability
These machines can handle flat, curved, and complex shapes using different tools and molds. This flexibility meets a wide range of design needs. - High-Precision Control
Advanced CNC systems ensure accurate, repeatable edge processing. Pre-set programs help deliver uniform results on every piece of glass. - Automated Operation
Automation allows the machine to run continuously with little human input. This saves time, lowers labor costs, and boosts productivity. - Built-In Safety Features
Safety shields and emergency stop buttons protect workers. Polished edges also reduce the risk of cuts during handling.
Key Features
- Edge Variety: Supports flat, round, beveled, chamfered, and other finishes
- Fast Processing: High-speed performance for better output
- Smart Controls: Easy-to-use touch screen and CNC system with saved programs
- Durability: Strong materials for long-term, stable use
- Flexible Settings: Adjustable for different glass sizes and thicknesses
Common Applications
Architectural Glass
Perfect for windows, partitions, and curtain walls—where both style and safety matter.
Automotive Glass
Used for windshields and car windows, ensuring clean fits and safe edges.
Furniture Glass
Ideal for table tops, mirrors, and shelving, enhancing both appearance and user safety.
Electronics
Used for screens and covers in devices, requiring exact sizing and edge quality.
Cost and Efficiency Benefits
Initial Investment
While the upfront cost is higher, the long-term savings from reduced labor and faster processing quickly make up for it.
Production Output
Automated edging increases production speed and capacity, helping you respond faster to market demands.
Better Quality Control
CNC precision reduces errors, lowers defect rates, and improves customer satisfaction.
Workplace Safety
Built-in safety features and polished edges lower the risk of injury and reduce health-related costs.
Choosing the Right Supplier
Understand Your Needs
Know what shapes, output volume, and level of precision you require.
Balance Your Budget
Choose a machine that fits your budget without sacrificing essential features.
Support and Service
Look for suppliers with strong after-sales support, including training, maintenance, and spare parts.
Check Their Reputation
Choose trusted suppliers with positive reviews, proven experience, and successful case studies.
Glass shape edging machines are essential for modern glass production. They offer a smart, efficient, and safe way to handle complex designs and large volumes. Investing in the right machine improves product quality, boosts output, reduces costs, and gives your business a strong competitive edge.